Стыковая сварка полиэтиленовых труб довольно часто используется во время монтажа трубопровода. Популярность данного метода обусловлена дешевизной и быстротой выполнения работ.
Общие сведения
При использовании данной технологии нагретые трубы соединяются под давлением и надежно фиксируются до тех пор, пока полностью не остынут. Прочность полученного соединения намного выше прочности труб.
Сварка полиэтиленовых труб встык применяется для изделий с диаметром от 50 мм. Именно при таком диаметре толщина их стенок составляет 5-7 мм, что является оптимальным значением для надежного соединения. Для изделий с меньшим диаметром использовать такой метод не стоит.
Виды полиэтиленовых труб
Стыковая сварка используется для соединения разных полиэтиленовых труб, которые отличаются между собой своей плотностью. Она обозначается цифрами, стоящими после аббревиатуры:
- ПЭ32. Имеют наименьшую плотность и поэтому практически нигде не используются.
- ПЭ63. Их часто используют для разводки водоснабжения в частных домах или же в безнапорных системах. Намного реже их применяют во время создания канализационных систем, так как они очень плохо справляются с сильным давлением и быстро ломаются.
- ПЭ80. Могут использоваться как внутри, так и снаружи. При наружном использовании их следует утеплять.
- ПЭ100. Данные изделия являются наиболее тяжелыми и прочными. Они применяются практически во всех областях. Довольно часто используют в разводке отопления и для доставки газов и жидкостей под сильным давлением.
Преимущества и недостатки
Стыковая сварка полиэтиленовых труб имеет немало преимуществ. Использование данного метода позволяет:
- проводить работы без большого количества людей и техники – для этого понадобится несколько человек и специальное оборудование для сварки полиэтиленовых труб встык;
- сэкономить время – встык выполняется довольно быстро;
- сократить затраты на монтаж трубопровода.
Недостатков у такого способа соединения не так уж и много. К ним можно отнести несколько ограничений:
- технология сварки полиэтиленовых труб встык требует много рабочего пространства, так как в стесненных условиях выполнять такую работу довольно сложно;
- не рекомендуется соединять изделия разной толщины, поэтому придется позаботиться о том, чтобы заготовки были одинаковыми;
- трубы нужно соединять так, чтобы одну из них можно было перемещать.
Некоторые из этих ограничений поможет обойти .
Особенности рабочего процесса
Для начала нужно узнать точные параметры сварки полиэтиленовых труб встык. С их помощью можно будет правильно настроить сварочное оборудование. Можно посмотреть параметры сварки полиэтиленовых труб встык в таблице.
Таблица параметров:
Разобравшись с таблицей сварки полиэтиленовых труб встык, необходимо подготовить оборудование. Для работы понадобятся:
- кусачки;
- рулетка;
- нагревательные насадки;
- паяльник, с помощью которого будет осуществляться сварка полиэтиленовых труб встык;
- крепежные болты для насадок;
- шаблон для отверстий;
- уровень, который может понадобиться для определения наклона соединяемых элементов.
Проводится с использованием различного сварочного оборудования:
- Ручное. Применяется, когда нужно соединить трубы малого диаметра. Перед использованием оборудования необходимо его настроить. Делается это при помощи таблицы сварки, в которой указаны все необходимые параметры. Именно от предварительной настройки зависит качество будущего сварного соединения.
- Полуавтоматическое. Такие агрегаты оснащаются специальными гидравлическими системами. Во время соединения элементов трубопровода используется центратор, который значительно облегчает работу. При помощи полуавтоматических моделей можно соединять изделия большого и малого диаметра.
- Автоматическое. Вся работа проходит под контролем компьютера. Сварщику даже не нужно заранее настраивать аппарат, так как он делает это самостоятельно. Использование автоматического оборудования позволяет полностью исключить ошибки, которые часто возникают при ручном соединении. Благодаря этому, качество сварочных стыков очень высокое.
Технология сварки
Чтобы правильно соединить элементы трубопровода, необходимо ознакомиться с особенностями данной технологии. Сварка полиэтиленовых труб встык выполняется следующим образом:
- Заготовки крепятся в центраторе сварочного оборудования, после чего осуществляется торцевание. Потом изделия прикладываются друг к другу, чтобы можно было убедиться в отсутствии сильного зазора. Если соединяются изделия с небольшим диаметром, то зазор должен быть меньше 0,4 мм.
- Между заготовками размещают сварочное зеркало, которое не должно разогреваться более 225 °C.
- Торцы элементов трубопровода прижимаются к зеркалу, пока не появится грат с высотой около 1 мм. После этого давление уменьшается до 0,3 кг/см 2 и не меняется до полного прогрева.
- После прогрева изделия соединяются друг с другом. При этом нужно следить за тем, чтобы грат не был слишком большим.
- Извлечь заготовки из центратора можно только после их остывания;
- В конце необходимо проверить трубопровод. Для этого нужно запитать его водой и убедиться в том, что она не протекает через стыки.
«Обратите внимание!
Сварка ПНД труб встык должна сопровождаться контролем параметров. Контролировать давление во время работы нужно при помощи манометра. Если такой возможности нет, то делает это придется визуально по размерам и форме грата.»
Во время монтажа трубопровода нужно учитывать то, что при изменении температур полиэтилен может сильно сжиматься или расширяться. Чтобы компенсировать температурные расширения, трубы рекомендуется укладывать змейкой.
Возможные ошибки
Во время соединения элементов трубопровода ручным способом могут быть допущены следующие ошибки:
- неравномерное распределение грата по окружности стыка;
- неправильное сваривание стыков, что может привести к их сильному смещению;
- плохое прижимание торцов, из-за чего на стыках могут быть поры и трещины.
Заключение
Сделать монтаж трубопровода при помощи стыковой сварки можно и самому. Для этого достаточно изучить параметры сварки полиэтиленовых труб встык и ознакомиться с особенностями данного процесса.
8 Параметры сварочного процесса
Казалось бы, с вводом в действие ГОСТ Р ИСО 55276 анархия кончилась. Или скоро кончится. Законными на территории РФ останутся только режимы стыковой сварки полиэтиленовых труб, описанные в ГОСТ.
Однако в Европе в извечной конкуренции между нормами DVS (Германской ассоциации сварщиков) и стандартами ISO чаще побеждают нормы DVS. Возможно, потому, что нормы DVS более пригодны для непосредственного использования. В частности, подготовка труб к сварочному процессу здесь нормирована в цифрах - и допустимое несовпадение стенок труб, и допустимый зазор между торцами. Температура нагретого инструмента (сварочного зеркала) здесь также описана подробно - в зависимости от материала трубы и толщины стенки. А не в виде широкого допустимого диапазона без пояснений.
В нашей стране нормам DVS тоже пока больше доверяют. Режимы стыковой сварки труб из ПЭ и ПП, регламентированные нормами DVS, соответствуют нашим нормативам, успешно применявшимся в течение десятилетий - ОСТ 6-19-505-79 и ВСН 003-88 и др.
В итоге европейские производители стыковых сварочных машин по умолчанию поставляют их со сварочными таблицами согласно нормам DVS, а российского потребителя это полностью устраивает.
Тем не менее, следует учитывать, что режимы стыковой сварки согласно ISO 21307 в Европе или согласно ГОСТ Р 55276 в России обладают не меньшей легитимностью, чем нормы DVS. И приводят в итоге к более-менее тому же результату, во всяком случае с точки зрения прочности и надежности сварного соединения. Осталось только понять, есть ли смысл отдавать им предпочтение и в каких случаях.
ГОСТ (и его прототип ISO) описывает 3 режима стыковой сварки – при единственном низком давлении, при двойном низком давлении, при единственном высоком давлении. Речь идет о давлении, создаваемом в материале свариваемых изделий на стадии формирования сварного шва и остывания. ГОСТ не дает разъяснения, в каких условиях какой из режимов предпочтителен. Некую ясность дает только пристальное изучение их особенностей.
8.1 Краткое сравнение режимов стыковой сварки
8.1.1 Первый режим – Сварка при единственном низком давлении
Этот режим стыковой сварки ПЭ труб можно назвать классическим, поскольку он очень близок к DVS 2207-1, ко всем другим национальным технологиям европейских стран, а также к режимам, когда-либо описанным в Российских нормативах. Возможно, поэтому его описание более, чем у других режимов сварки полиэтиленовых труб, пригодно для непосредственного использования сварщиком.
Существенные отличия от двух других режимов сварки, описанных в ГОСТ:
- По сравнению с третьим режимом стыковой сварки, первый режим может выполняться на более дешевом оборудовании. Поскольку регламентированное сварочное давление – всего 1,7 кгс/см 2 (в DVS 2207-1 похоже: 1,5 кгс/см 2) . Существенно ниже просто нельзя, иначе обеспечить прочность сварки уже будет нельзя ни удлинением времени, ни увеличением температуры нагревателя. Самое низкое сварочное давление обозначает, что нет необходимости в безумно прочном центраторе и чрезмерно мощном гидравлическом агрегате. Расплата за это – несколько большей продолжительностью цикла сварки стыкового соединения.
- По сравнению со вторым режимом стыковой сварки, первый режим требует длительного поддержания давления на фазе остывания. Это позволяет снизить температуру нагретого инструмента, уменьшить время нагрева, а главное – сократить общую продолжительность цикла сварки стыкового шва.
8.1.2 Второй режим – Сварка при двойном низком давлении
Этот режим стыковой сварки полиэтиленовых труб разработан для сварочных аппаратов, которые не только не могут обеспечить сварочное давление выше 1,5 кгс/см 2 , но даже такое давление могут поддерживать только в течение короткого времени.
Существенные отличия от двух других сварочных режимов, описанных в ГОСТ:
- По сравнению с третьим режимом стыковой сварки, второй режим не требует дорогостоящего оборудования, способного создавать высокое сварочное давление.
- По сравнению с первым режимом стыковой сварки, второй режим не требует длительного поддержания сварочного давления – всего лишь 10 сек в начале остывания. Для того чтобы такое непродолжительное сжатие обеспечивало удовлетворительную прочность шва, пришлось увеличить температуру нагретого инструмента и время нагрева.
По нашему мнению, второй режим стыковой сварки практической ценности не имеет по двум причинам: (1) за долгую практику продаж сварочного оборудования и изучения оборудования конкурентов нам не приходилось встречать аппаратов, не способных поддерживать давление в течение длительного времени, а главное (2) второй режим стыковой сварки и в ГОСТе, и в первоисточнике ISO 21307 описан противоречиво и вряд ли пригоден для практического применения. Поэтому далее рассматривать его не будем.
8.1.3 Третий режим – Сварка при единственном высоком давлении
Этот режим стыковой сварки полиэтиленовых труб сводит продолжительность сварки стыковых соединений к минимуму, не обращая внимания на повышенные требования к оборудованию. А производители оборудования – извольте соответствовать.
Существенные отличия от обоих других режимов стыковой сварки, описанных в ГОСТ:
- Третий режим сокращает чистое время сварочного процесса в 2.0-2.5 раза (см.п.8.3). И это безусловный плюс.
- Третий режим требует сварочное давление 4,2÷6,2 кгс/см 2 . Это в 3 раза выше, чем у первого режима. И в 3.5 раза выше, чем у DVS 2207-1. Это обстоятельство имеет две стороны медали. С одной стороны, для сварки большой трубы (близко к верхнему пределу рабочего диапазона сварочной машины) потребуется в разы более крепкий центратор и более мощный гидравлический агрегат. Другими словами, более дорогая машина. Но с другой стороны, при сварке маленькой трубы (близко к нижнему пределу рабочего диапазона сварочной машины или немножко ниже диапазона) третий режим оказывается настоящим спасением!
8.2 Сравнение параметров сварки ПЭ труб при низком и высоком давлении
8.2.1 Температура нагревателя
Температура T
нагретого инструмента имеет значение для двух фаз сварочного процесса – фаза 1 (оплавление) и фаза 2 (нагрев). Далее нагретый инструмент убирается из зоны сварки и больше в процессе не участвует.
Главное и единственное назначение нагретого инструмента – нагреть торцы труб.
График распределения температуры по оси трубы непрерывно изменяется в течение всего сварочного процесса. Нас сейчас интересует, какой будет температура свариваемых торцов в момент их касания после удаления нагретого инструмента (технологическая пауза).
8.2.3 Максимально допустимое время технологической паузы
Допустимая продолжительность t 3 технологической паузы ограничивается двумя основными процессами, происходящими с нагретым полимером на воздухе – остывание и окисление. Если не уложиться в регламентированное время, то торцы труб либо не слипнутся при сварочном давлении, либо тонкий слой материала в зоне шва будет окисленным, непрочным.
У горячего полиэтилена окисление сравнительно небольшое, ограничение времени технологической паузы определяется в основном процессом остывания – в отличие, например, от ПВХ , у которого основные разрушения приносит окисление. Таким образом, для полиэтилена максимально допустимое время технологической паузы определяется скоростью остывания (зависит от толщины стенки) и минимально допустимой итоговой температурой (зависит от дальнейшего сварочного давления).
Для первого режима стыковой сварки полиэтилена (низкое давление сварки) ГОСТ определяет максимальную продолжительность технологической паузы в секундах формулой 0,1 +4, для третьего режима (высокое давление сварки) – 0,1 +8.
DVS 2207-1 приводит максимальную продолжительность технологической паузы в виде таблицы, которую можно интерполировать похожей функцией с сохранением того же принципа: чем больше толщина стенки, тем больше допустимое время перестановки.
8.2.4 Величина сварочного давления
После нагрева и технологической паузы распределение температуры по оси трубы соответствует графику на рис.25. Где горячее, там материал больше подвергся термодеструкции. И после остывания будет менее прочным.
Как же не потерять прочность трубы при менее прочном материале? Выход один – увеличить толщину стенки трубы в этом месте.
![]() |
Если мысленно разбить трубу на участки очень малой длины (рис.29), то станет понятным, что каждый участок был нагрет до вполне определенной температуры, соответственно, претерпел вполне определенное ухудшение прочностных свойств в результате этого нагрева, и требует вполне определенного относительного увеличения толщины стенки для компенсации этого ухудшения. Чтобы достичь такого неравномерного увеличения толщины стенки, свариваемые трубы необходимо с усилием прижать друг к другу, пока нагретые слои не остыли. Тогда каждый участок трубы «расплющится» и увеличит толщину стенки тем больше, чем больше он был нагрет и чем большую термодеструкцию претерпел. Всё понятно, логично и целесообразно. С каким же усилием необходимо прижать трубы друг к другу, чтобы увеличение толщины стенки в каждом сечении компенсировало ухудшение прочностных свойств материала в этом сечении? Понятно, что величина относительного расширения зависит от сварочного давления. Т.е. при одинаковом нагреве режим стыковой сварки при высоком давлении даст большее увеличение толщины стенки, чем режим сварки при низком давлении. Однако следует помнить, что во время дальнейшего остывания полиэтилен сохраняет эластичность, которая снижается со снижением температуры. И после снятия сварочного давления достигнутое нами утолщение стенки несколько отыграет назад. Чем раньше снимем давление, тем сильнее отыграет. Подробнее об этом – в п.8.2.6 . |
---|---|
Рис. 29 Распределение нагрева |
Малое сварочное давление (1,5-1,7 кгс/см 2) рассчитано на то, что такое давление будет действовать, пока температура полиэтилена не снизится до 40-45°C.
А увеличение толщины стенки при сварочным давлении 4,2-6,2 кгс/см 2 будет гораздо больше. Тогда остывание под давлением можно закончить гораздо раньше, остаточного увеличения толщины стенки все равно будет достаточно.
8.2.5 Время осадки
По истечении технологической паузы сварочное давление достигается не мгновенно, а занимает некоторое время, называемое фазой осадки, или фазой подъема давления. Хотя бы потому, что ни один привод не способен выполнить такую работу мгновенно. Но есть и другая причина.
Снова рассмотрим график распределение температуры в момент касания труб после технологической паузы (рис.25). Как видим, тонкий слой материала находится в вязко-текучем состоянии, т.е. имеет температуру выше T ВТ . Это необходимое условие, мы к этому специально стремились, иначе торцы труб не слипнутся при контакте.
Если мы теперь резко создадим сварочное давление, в этом тонком слое будет особенно сильное течение выдавливаемого материала. Это течение материала бессмысленно увеличит наружный и внутренний грат, что, в частности, снизит проходимость трубопровода в месте стыкового сварного шва (рис.30).
Но главная проблема – в другом. Направленное течение термопласта в тонком зазоре приведет к последующей направленной кристализации полиэтилена, что снизит прочность трубопровода на разрыв вдоль оси трубы.
Короче говоря, нельзя допустить выраженного течения материала в тонком зазоре. А это значит, что полное сварочное давление можно применять только когда немного остынет наш самый горячий тонкий слой материала. А именно, когда он успеет отдать часть тепла соседним слоям материала (рис.31).
На это перераспределение тепла уходят считанные секунды. Очевидно, что чем больше толщина стенки трубы и, соответственно, чем больше глубина прогрева торцов и чем толще слой вязко-текучего материала, тем это перераспределение тепла занимает больше времени. Для первого режима сварки полиэтиленовых труб (низкое давление сварки) ГОСТ Р ИСО 55276 определяет его в секундах формулой 0,4 +2.
Однако есть противоположная опасность. Если сварочное напряжение создать с большой задержкой, его величина может оказаться недостаточной для утолщения остывшей стенки. И эта опасность страшнее возможного увеличения грата и направленной кристаллизации. Поэтому ГОСТ называет указанное время осадки «максимальным».
8.2.6 Время остывания
Когда мы сжимаем трубы на фазе 4 (осадка) силой F 5 и поддерживаем созданное сварочное давление в течение фазы 5 (остывание), характер деформации материала в зоне нагрева – одновременно пластический (необратимый) и эластический (обратимый). Под воздействием сварочного давления стенка трубы утолщается, продолжая упруго сопротивляться силе F 5 .
Если в какой-то момент мы уберем сжимающую силу F 5 , наша деформация заметно вернется назад (рис.32).
Чем позже мы уберем усилие прижима, тем меньше вернется назад наша деформация. Объясняется это просто. По мере остывания термопласта силы Ван-дер-Ваальса, действующие между звеньями соседних макромолекул, начинают преобладать на силами теплового колебания звеньев. Можно упрощенно сказать, что материал твердеет в том положении, в котором его насильно удерживают.
До какой же температуры необходимо остудить материал, чтобы можно было убрать сжимающую силу F 5 и не бояться, что деформация вернется назад слишком сильно? Все зависит от того, насколько большая деформация была создана вначале, т.е. какое сварочное давление ее вызвало. Если увеличение толщины стенок изначально было создано низким сварочным давлением (1,5-1,7 кгс/см 2), то запаса практически нет, остужать придется до температуры 40-45°C. Для первого режима сварки полиэтиленовых труб (низкое давление сварки) ГОСТ определяет минимально допустимое время остывания в минутах формулой +3.
А если изначально увеличение толщины стенок было вызвано высоким сварочным давлением (4,2-6,2 кгс/см 2), то, согласно ГОСТ, остывание под давлением можно закончить через (0,43) минут, остаточное утолщение стенки все равно будет достаточным для компенсации термодеструкции, возможного несовпадения стенок труб и возможных ошибок оператора. Вот откуда берется экономия времени у третьего сварочного режима.
Далее общее правило для любых сварочных режимов: ни в коем случае нельзя пытаться ускорить процесс остывания, поливая зону сварного соединения водой, или другими методами. Это приведет к созданию внутренних напряжений в материале и, в результате, к общему ослаблению сварного соединения. Чтобы наглядно проиллюстрировать, как это работает, возьмем горячую полиэтиленовую пластину и мысленно разобьем ее на 2 слоя – верхний и нижний (рис.33). Если мы теперь сверху польем пластину водой, верхний слой быстро остынет. Поскольку полимеры имеют высокий коэффициент температурного расширения, верхний слой при остывании уменьшится в размерах. Нижний слой пока горячий и мягкий, он мало препятствует сокращению размеров наружного слоя; вместо этого он сам без особого сопротивления уменьшает свою длину и увеличивает толщину. Поэтому пластина выгнется вниз совсем незначительно.
Теперь начинает остывать нижний слой. При остывании он также стремится уменьшить все свои размеры. Однако остывший твердый верхний слой упруго сопротивляется уменьшению длины. В результате пластина очень заметно выгнется вверх.
А вот у стенки трубы (в т.ч. в зоне сварного шва) нет возможности выгнуться. В случае охлаждения водой она сохранит форму, но внутренний слой будет растянут, как пружина. Это сильно ослабляет стенку трубы. Правда, справедливости ради следует сказать, что в полиэтилене внутренние напряжения исчезают очень быстро. Через 2-3 года от них не останется и следа. Если только за это время давление воды (или газа) внутри трубы не порвет наш сварной шов, ослабленный внутренними напряжениями.
8.2.7 Давление оплавления; высота первичного валика
Теперь вернемся к началу сварочного процесса.
Когда торец трубы впервые касается сварочного зеркала, необходимо как можно скорее достичь полного теплового контакта между поверхностями торца трубы и сварочного зеркала. Единственный способ сделать это – прижать трубу к сварочному зеркалу со значительным усилием, чтобы оплавляемый материал начал течь и вытеснять воздух из пустот. При этом некоторое количество расплавленного материала выдавливается по всему периметру торца трубы в виде наружного и внутреннего грата, что является наглядным свидетельством «подгонки» поверхности торца трубы к поверхности сварочного зеркала (рис.18).
Давно разработанные режимы стыковой сварки (в т.ч. DVS) были придирчивы к форме получившегося первичного валика, по этой форме косвенно определялось давление, при котором он был создан. Первичный валик в форме острого лепестка (рис.34) свидетельствовал о слишком высоком давлении на первой фазе сварки и считался ошибкой.
Действительно, старые одномодальные марки полиэтилена вели себя именно так, а острый лепесток, теоретически, создавал «концентратор напряжений» во внутреннем углу. Однако современные би- и полимодальные марки полиэтилена отличаются плавной термомеханической кривой, их текучесть более плавно увеличивается с ростом температуры и давления. Форма первичного валика при давлении, явно превышающем 1,5-1,7 кгс/см 2 , может быть самой неожиданной, от капли до плоского столбика. В результате форму первичного валика оставили в покое, а вместе с этим любое давление на фазе оплавления торцов перестали считать ошибкой.
Теперь логика при выборе давления оплавления – следующая. Маленькое давление нежелательно, иначе формирование первичного валика займет слишком много времени. Кроме того, с точки зрения удобства управления сварочным аппаратом, проще перед началом сварки стыкового шва один раз настроить регулировочный клапан на определенное сварочное давление, и затем использовать это давление как при оплавлении торцов, так и при формировании сварного шва.
Интересно, что для третьего режима стыковой сварки (высокое сварочное давление) размер первичного валика в ГОСТе не определен. Зато определен (опять же, в миллиметрах) размер валика, который должен получиться по окончании нагрева: 0,15 +1. Это одна из причин, по которым сварщик не может непосредственно использовать описание режима стыковой сварки при высоком давлении – невозможно понять, при каком первичном валике закончить оплавление (сбросить давление), чтобы по окончании нагрева получить валик предписанного размера. Можно сделать предположение, что при нагреве размер валика увеличивается незначительно, и ориентироваться на указанный размер вторичного валика уже при оплавлении. Однако оставим это разработчикам технологических карт сварки полиэтиленовых труб.
8.2.8 Давление нагрева
Главная задача фазы нагрева – прогреть торцы труб на нужную глубину. Это значит, что давление нагрева должно быть достаточно малым, чтобы размер валика больше не увеличивался. В теории – давление должно быть нулевым.
Но это только в теории. При практическом применении нулевое давление нагрева может привести к нечаянной потере контакта между торцом трубы и нагревателем. Особенно если давление перемещения мало и/или если давление перемещения определяется не трением (или не только трением), а сползанием трубы с наклонного склона.
Теоретическая часть описания обеих процедур в ГОСТ рекомендует давление нагрева в диапазоне от 0 до давления перемещения. Однако пример, приведенный ниже в ГОСТ, устанавливает давление нагрева на уровне 0,25 кгс/см 2 сверх давления перемещения, и такая величина пригодна для практического применения.
8.3 Сравнение длительности сварки при низком и высоком давлении
Для оценки выигрыша во времени сварки полиэтиленовых труб, который обеспечивает третий режим стыковой сварки (при высоком давлении) по сравнению с первым режимом (при низком давлении) попробуем сравнить время сварки при разных режимах для труб с одинаковой толщиной стенки.
При этом не учитываем время оплавления, время технологической паузы и время осадки. Эти времена малы и не до конца определены. А главное – они вносят разнонаправленный «довесок» в общую продолжительность сварки (оплавление короче при высоком давлении, а технологическая пауза и осадка короче при низком давлении), поэтому для грубого сравнения двух процедур ими можно пренебречь.
Сварочный процесс |
Толщина стенки |
Время нагрева |
Время остывания |
Общее время |
---|---|---|---|---|
Низкое давление | ||||
Высокое давление | ||||
Низкое давление | ||||
Высокое давление | ||||
Низкое давление | ||||
Высокое давление |
Видим, что для труб с малой толщиной стенки режим стыковой сварки при высоком давлении дает выигрыш времени сварки стыка более чем в 2,5 раза. Для средних толщин – примерно в 2 раза. Для больших толщин – чуть менее, чем в 2 раза.
Это только чистое время сварки стыка полиэтиленовых труб. Если учесть время подготовки к сварке стыка – фиксацию труб, торцовку, проверку соосности и пр. – мы, тем не менее, получим оценочную разницу времени в 1,3-1,6 раза. Другими словами, там, где традиционная технология стыковой сварки может сделать 10 стыков в день, процедура сварки при высоком давлении может сделать 13-16 стыков.
ВЫВОД: Принимая во внимание, что стоимость оборудования для стыковой сварки по традиционной технологии и аналогичного оборудования для сварки при высоком давлении отличается примерно в 1,2-1,3 раза, сварка при высоком давлении имеет прямой смысл.
Есть еще мнение, что высокое сварочное давление позволит справиться с «капризами» нестекающих марок полиэтилена. Однако это пока только гипотеза.
ВНИМАНИЕ! Мы привыкли к тому, что по окончании сварки по традиционной технологии (при низком давлении) сварной шов уже остыл до 40-45°C и не боится физических нагрузок. При использовании третьего сварочного режима (при высоком давлении) следует помнить, что по окончании остывания под давлением зона сварки еще довольно горячая, поэтому трубопровод после извлечения из центратора еще некоторое время требует аккуратного обращения.
Годовой (с весны 2014г.) опыт продаж оборудования для сварки полиэтиленовых труб при высоком сварочном давлении показал, что Российские потребители не спешат массово переходить на него, а по-прежнему предпочитают машины для стыковой сварки по традиционной технологии . Автор видит для этого две возможные причины:
- Режим стыковой сварки при высоком сварочном давлении разработан только для труб из полиэтилена, в то время как для стыковой сварки полипропиленовых, ПВДФ и ПБ труб самыми популярными по-прежнему остаются режимы сварки DVS с низким сварочным давлением. И реализация этих сварочных режимов неудобна на машинах с избыточно мощной гидравликой.
- В любом ответственном деле новшества воспринимаются с осторожностью. В основном из-за недостатка информации.
Сварка встык нагретым инструментом заключается в нагревании свариваемых торцов труб или деталей до вязкотекучего состояния полиэтилена при непосредственном контакте с нагретым инструментом ипоследующем соединении торцов под давлением осадки после удаления инструмента.
Основными параметрами процесса сварки встык являются:
– температура нагретого инструмента Т н;
– продолжительность оплавления t оп и нагрева t н;
– давление нагретого инструмента на торцы при оплавлении Р оп и нагреве Р н;
– продолжительность технологической паузы между окончанием нагрева и началом осадки t п;
– давление на торцы при осадке Р ос;
– время охлаждения сваренного стыка под давлением осадки t охл.;
Для машин со средней и высокой степенью автоматизации дополнительным нормируемым параметром может являться время нарастания давления осадки t Д
Изменение величины параметров по времени в процессе сварки производят по циклограмме, рис.7.
Технологические параметры сварки выбирают по таблицам 1 – 4 в соответствии с маркой полиэтилена, из которого изготовлены трубы и детали.
Температуру рабочей поверхности нагретого инструмента выбирают по таблице 4 взависимости от материала свариваемых труб (ПЭ 80, ПЭ 100).
Продолжительность оплавления t оп. , как правило, не нормируется и зависит от появления первичного грата.
Оплавление и нагрев торцов свариваемых труб и деталей осуществляют одновременно (синхронно) посредством их контакта с поверхностями нагретого инструмента.
Оплавление торцов необходимо выполнять при давлении
Р оп = 0,2 ± 0,02
МПа
(2,0±
0,2 кгс/см 2), в течение времени t оп достаточного для образования по всему периметру, контактирующих с нагревателем торцов труб валиков расплавленного материала (первичного грата) высотой не менее:
– 1,0 мм при толщине стенки труб от 5 до 10 мм;
– 1,5 мм при толщине стенки труб от 10 до 12 мм;
– 2,0 мм при толщине стенки труб от 12 до 20 мм;
– 2,5 мм при толщине стенки труб от 20 до 26 мм;
– 3,0 мм при толщине стенки туб от 26 до35 мм.
После появления первичного грата давление необходимо снижать до Р н = (0,02±0,01) МПа (0,2±0,1 кгс/см 2) и торцы нагревать в течение времени t н, которое в зависимости от сортамента (толщины стенки) труб, температуры окружающего воздуха Т о следует выбирать по табл. 5.
Таблица 4.
Температура рабочей поверхности нагретого инструмента, ºС
Таблица 5.
Время нагрева торцов труб t н, с, из ПЭ80 и ПЭ100
Температура окружающего воздуха Т о, ºС и время прогрева, с | ||||
От минус 15 до 0 | От 0 до 20 | От 20 до 45 | ||
SDR 11 | 63х5,8-75х6,8 | 75-110 | 60-105 | 50-.95 |
90х8,-110х10,0 | 100-140 | 85-140 | 70-125 | |
125х11,4-140х12,7 | 120-170 | 100-165 | 80-150 | |
160х14,6-180х16,4 | 155-210 | 135-200 | 105-185 | |
200х18,2-225х20,5 | 190-260 | 160-250 | 125-225 | |
250х22,7-315х28,6 | 250-360 | 225-350 | 210-310 | |
SDR 17,6 | 90х5,2-110х6,3 | 70-105 | 55-100 | 45-90 |
125х7,1-140х8,0 | 95-125 | 80-120 | 60-110 | |
160х9,1-180х10,3 | 105-140 | 90-140 | 70-125 | |
200х11,4-225х12,8 | 120-170 | 100-165 | 80-150 | |
250х14,27-315х18,5 | 135-200 | 115-190 | 90-180 |
Допускается давление Р н снижать до минимума при сохранении постоянства контакта торцов труб (деталей) с нагретым инструментом.
Продолжительность технологической паузы, необходимой для удаления нагретого инструмента, должна быть минимальной, не более:
– 3 с – для труб Ø 63 мм;
– 4 с - для труб от Ø 90 до 140мм;
– 5 с - для труб от Ø 140 до 250мм;
6 с – для труб от Ø 250 до 315 мм.
После удаления нагретого инструмента торцы труб или труб идеталей сводят и производят осадку стыка при давлении Р ос = (0,2±0,02) МПа (2,0±0,02 кгс/см 2). Осадку стыка необходимо осуществлять плавным увеличением давления до заданного уровня. Время нарастания давления осадки t д, с, для труб из ПЭ 80, ПЭ 100, следует принимать по табл.6.
Охлаждение стыка необходимо производить под давлением осадки в течение времени t охл. , величина которого принимается по табл. 7. в зависимости от толщины стенки свариваемых труб и деталей и температуры окружающего воздухе Т о.
Таблица 6.
Время нарастания давления осадки t д, с, для труб из ПЭ80, ПЭ100
Сортамент свариваемых труб по ГОСТ Р 50838 | Времяt д, с | |
Стандартное размерное отношение | Диаметр и толщина стенки трубы, мм | |
SDR 11 | 63х5,8-75х6,8 | 3-7 |
90х8,2-110х10,0 | 4-8 | |
125х11,4-140х12,7 | 4-11 | |
160х14,6-180х16,4 | 6-12 | |
200х18,2-225х20,5 | 8-14 | |
250х22,7-315х28,6 | 10-16 | |
SDR 17,6 | 90х5,2-110х6,3 | 3-6 |
125х7,1-140х8,0 | 4-7 | |
160х9,1-180х10,3 | 4-8 | |
200х11,4-225х12,8 | 5-10 | |
250х14,27-315х18,5 | 8-12 |
Таблица 7.
Время охлаждения стыка t охл., мин, не менее, для труб из ПЭ80 и ПЭ100
Сортамент свариваемых труб по ГОСТ Р 50838 | Температура окружающего воздуха Т о, ºС, и время прогрева, с | |||
Стандартное размерное отношение | Диаметр и толщина стенки трубы, мм | От минус 15 до 0 | От 0 до 20 | От 20 до 45 |
SDR 11 | 63х5,8--75х6,8 | 4-5 | 5 -6 | 6-7 |
90х8,2--110х10,0 | 6-7 | 7-8 | 8-9 | |
125х11,4--140х12,7 | 8-11 | 10-13 | 12-15 | |
160х14,6--180х16,4 | 11-14 | 13-16 | 15-18 | |
200х18,2--225х20,5 | 16-21 | 18-23 | 20-25 | |
250х22,7--315х28,6 | 24--30 | 26-.32 | 28-36 | |
SDR 17,6 | 90х5,2--110х6,3 | 4-5 | 5-6 | 6-7 |
125х7,1--140х8,0 | 5-6 | 6-7 | 8-9 | |
160х9,1--180х10,3 | 8-10 | 9-12 | 10-12 | |
200х11,4--225х12,8 | 10-11 | 11-13 | 13-15 | |
250х14,27--315х18,5 | 18-22 | 19-24 | 21-28 |
С целью повышения точности поддержания заданных давлений (Р оп., Р н, Р ос) в процессе сварки необходимо учитывать потери на трение движущихся частей сварочной машины иперемещаемой при сварке трубы (секции). Для этого перед сваркой каждого стыка производят замер усилия при холостом ходе подвижного зажима центратора машины с закреплённой в нем трубой (секцией), которое суммируют с усилием, необходимым для создания заданных давлений (Р оп., Р н, Р ос).
При сварке нагретым инструментом рабочие поверхности нагревателя покрывают антиадгезионным слоем, препятствующим налипанию расплава на инструмент.
Параметры циклограммы процесса (рисунок 7) и режимы сварки (таблицы 4 – 7) труб различного сортамента соблюдаются сварочной машиной с высокой степенью автоматизации автоматически, со средней степенью автоматизации – часть параметров выполняется в ручном режиме, в ручных сварочных машинах автоматически поддерживается только температура нагревательного инструмента.
Маркировку сварных стыков (код оператора) производят несмываемым карандашом - маркером яркого цвета (например: белого или желтого – для черных труб, черного и голубого - для желтых труб).
Маркировку (номер стыка и код оператора) наносят рядом со стыком со стороны, ближайшей заводской маркировке труб.
Допускается маркировку (код оператора) производить клеймом на горячем расплаве грата через 20-40 с после окончания операции осадки в процессе охлаждения стыка в зажимах центратора сварочной машины в двух диаметрально противоположных точках. Рекомендуется использовать клейма типа ПУ-6 или ПУ-8 по ГОСТ 2930.
При выполнении работ проводить систематический операционный контроль качества сборки под сварку и режимов сварки;
Подготовка к работе и порядок работы. На месте производства работ свариваемые трубы зафиксировать в неподвижном и подвижном зажимах сварочного блока. Концы должны выступать от 15-20 мм. Детали фасонного профиля, переходы и втулки фиксируются только в подвижном зажиме, вспециальных вкладышах, которые поставляются со сварочным блоком и устанавливаются взамен вкладышей 14. (рис. 4). При переходе от трубы большегодиаметра к меньшему, переходную втулку предварительно приварить к трубеменьшего диаметра. На штоки цилиндров установить торцовочное устройствоизафиксировать. Ручкой 10 (рис. 4) плотно поджать к торцовочному устройствуторцы закрепленных труб. Поворотом рукоятки торцовочного устройства производится подрезка торцов обеих труб. Одновременно с торцовкой труб производится нагрев нагревателя (поверхности нагревателя должны бытьочищены от наплавлений скребком).
Контроль температуры его нагрева осуществляется автоматически. Индикатор находится в нагревателе до тех пор, пока на его шкале стрелка не остановит в пределах отмеченного сектора, при этом для труб из полиэтилена средней плотности ПСП стрелка должна находиться в начале сектора (TH-230-240º С), а для труб из полиэтилена высокой плотности ПВП в конце сектора (ТН-250-260º С). После определения температуры, индикатор вынимается из отверстия нагревателя и вставляется в скобу, предусмотренную на кожухе горелки. Затем нагреватель устанавливается в зазор между обработанными торцами изделий. Перемещением подвижного зажима вручную с помощью механизма ручного перемещения производится прижим торцов к плоскостям нагревателя.
Кран гидросистемы перекрывается и насосом создается требуемое давление. После оплавления торцов быстро сбрасывается давление в гидросистеме и насосом создается давление, необходимое для прогрева. После прогрева снова сбрасывается давление. Для этого необходимо открыть кран 19 (рис. 4) и убрать нагреватель. Трубы быстро с помощью ручного привода сводятся до соприкосновения, кран закрывается и насосом 11 создается необходимое давление.
Контроль давления осуществляется по манометру с предельными отклонениями 20%. Показания манометра должны складываться из двух величин по формуле:
Р раб = Р расч + Р хол. хода
где Р раб. – рабочее давление, кгс/см 2 ; Р расч – давление, необходимое для создания усилия прижима свариваемых поверхностей при оплавлении, прогреве или осадке материала, кгс/см 2 . Оно выбирается в зависимости от диаметра и типа свариваемых труб по таблице 4.
Р хол. хода – давление в системе, необходимое для преодоления сил трения в подвижном зажиме (усилие холостого хода), кгс/см 2 . Оно определяется через 200 часов работы установки, т.к. эта величина зависит от состояния трущихся поверхностей.
Трубы после сварки должны быть выдержаны в зажимах сварочного блока в течение 5-7 минут для охлаждения, после чего трубы освобождаются из зажимов и установка передвигается к месту сварки нового стыка. Допускается торцовку труб производить следующим образом. При помощи гидравлической системы подвести концы труб к торцовочному устройству, обеспечив оптимальный прижим для снятия стружки, торцовку производить до прекращения выхода стружки. При необходимости поджим концов труб к торцовочному устройству повторить и вновь произвести торцовку.
Оборудование и материалы
1. Установка для сварки нагретым инструментом, принципиальная схема которой представлена на рис.4.
2. Заготовки из труб термопласта размером 63×5,8 мм(один из материалов – полиэтилен, винипласт, оргстекло) – 10 шт.
3. Машина для испытания на растяжение усилием до 15000 Н, оснащенная специальными захватами.
4. Инструмент для изготовления образцов: шаблон, чертилка, ножовка, полукруглый напильник, штангенциркуль, шабер.
Порядок выполнения работы
1. Ознакомиться с инструкцией по работе с установкой мобильной для сварки полиэтиленовых труб.
2. Произвести опытную сварку одной заготовки с целью проверки работы установки и получения навыка настройки ее на определенный режим.
3. Провести маркировку и замеры свариваемых сечений для подсчета необходимой величины усилий во время сварки. Данные занести в табл. 8.
4. Сварить заготовки при четырех-пяти различных значениях одного из параметров и неизменной величине остальных (по указанию преподавателя).
При креплении труб в хомутах обращать внимание на правильность установки заготовок. Смещения кромок не допускать.
5. После охлаждения сварного шва (время охлаждения не менее 1 мин)освободить заготовки от верхних зажимов, отвести подвижный хомут в исходное положение и снять заготовку с установки.
6. Провести визуальный контроль полученного сварного соединения.Критерии оценки внешнего вида соединений, выполненных нагретым инструментом встык, приведены в таблице 26 приложения А.
Таблица 8
Результаты измерений
№ пп. | Материал заготовок | Размеры заготовок до сварки | Режим сварки | Разрывное усилие, Н | Предел прочности при растяжении, МПа | Относительная прочность, % | Характер разрушения | Форма и размер грата, мм | |||||||||
Ширина | Высота | ||||||||||||||||
Толщина, см | Средний диаметр, см | Площадь, см 2 | Температура инструмента, ºС | Время, с | Давление, МПа | ||||||||||||
Оплавления | Нагрева | Оплавления 0,2±0,02 | Нагрева 0,02±0,01 | ||||||||||||||
Вопросы для самопроверки:
1.Назовите разновидности стыковой сварки термопластов нагретым инструментом?
2. Составные части установки для сварки полиэтиленовых труб?
3.Назовите основные параметры процесса сварки встык?
4.Циклограмма процесса сварки встык нагретым инструментом труб из полиэтилена?
5. В зависимости от чего выбирают температуру рабочей поверхности нагретого инструмента?
6. От каких факторов зависит время нагрева торцов труб при сварке НИ?
7. От каких факторов зависит время охлаждения стыка?
8. Что такое технологическая пауза?
9. От каких факторов зависит время технологической паузы?
10. Какую величину составляет давление при оплавлении торцов труб?
11. Что называют гратом?
12. Какой высоты должны быть валики первичного грата при толщине стенки труб от 10 до 12 мм?
В данной статье приведена технология сварки полиэтиленовых труб, а также труб из пластика, пвх и других полимерных материалов. Особое внимание уделено следующим вопросам:
ОПРЕДЕЛЕНИЕ ПОНЯТИЯ СВАРКИ
С варные соединения являются неразъемными, т.е. не могут быть разобраны без поломки деталей. Это свидетельствует о монолитности (сплошности) сварных соединений. Такая монолитность может быть обеспечена, если между поверхностными макромолекулами соединяемых деталей возникнут силы взаимодействия (силы Ван-дер-Ваальса) и произойдет их взаимное перемещение из одной детали в другую, например за счет диффузии.
Казалось бы, достаточно сблизить поверхности на такие расстояния (0,3-0,4 мм), на которых начинают заметно проявляться эти силы, чтобы между поверхностными макромолекулами свариваемых пластмасс возникли связи, исчезла граница раздела и произошла сварка. Именно этими соображениями руководствуются некоторые авторы, определяя сварку как технологический процесс получения неразъемного соединения частей изделия, основанный на взаимной диффузии и химическом взаимодействии макромолекул полимеров, в результате которых между соединяемыми поверхностями исчезает граница раздела.
Однако даже в идеальном случае, когда на соединяемых поверхностях отсутствуют микронеровности (идеально гладкие поверхности), различные загрязнения, адсорбированные газы и другие составляющие, препятствующие такому сближению, необходима затрата извне деформационной и тепловой энергии. Деформационная энергия будет затрачиваться на преодоление сил отталкивания, возникающих между сближаемыми поверхностными атомами. Тепловая энергия увеличивает вероятность развития взаимодействия между ними. Если исходить из таких представлений, то в сварочной зоне можно выделить два основных процесса: первый - подвод и преобразование энергии и второй - движение (или превращение) вещества. Интенсивность процесса преобразования энергии и его характер определяют вид сварки .
Для осуществления процесса сварки необходима активация свариваемых поверхностей. Это достигается за счет подвода и, в некоторых случаях, преобразования энергии. Введение вещества необходимо только при некоторых видах сварки пластмасс, например при сварке нагретым газом с применением присадочного материала, а также при сварке расплавом. В последнем случае с присадочным материалом и расплавом подводится и энергия.
Движение вещества при различных видах сварки пластмасс может быть значительным. Оно обусловлено перемешиванием и диффузией, протекающими в материале, нагретом до вязкотекучего состояния. Особым видом движения следует считать химическую реакцию активных групп, расположенных на свариваемых поверхностях, между собой или с активными группами промежуточного вещества, которая также может протекать при подводе энергии того или иного вида (химическая сварка) .
Исходя из сказанного, можно считать, что в термодинамическом смысле не может быть разницы в определении сварки пластмасс и металлов. Это определение может быть сформулировано следующим образом: сварка - это процесс получения монолитного соединения материалов за счет введения и термодинамически необратимого преобразования энергии и вещества в месте соединения .
МЕХАНИЗМ ПРОЦЕССА СВАРКИ И СВАРИВАЕМОСТЬ ПЛАСТМАСС
С огласно современным представлениям, процесс сварки следует рассматривать как топохимическую реакцию, т.е. химическую реакцию, протекающую по поверхности твердого тела. В основе любой химической реакции лежит процесс разрыва связей в исходных веществах и возникновения новых связей, приводящий к образованию нового вещества. Таким образом, механизм образования соединения не должен меняться при переходе от одного способа сварки к другому и от одного материала к другому. Изменяется только совокупность явлений на контактных поверхностях, приводящая их в состояние взаимодействия. Эти явления могут быть различными и определяются природой материала и способом сварки .
Для топохимической реакции характерно протекание в три стадии: образование физического контакта; активация контактных поверхностей; объемное развитие взаимодействия.
Образование физического контакта происходит обычно при приложении к свариваемым деталям давления. В отдельных случаях, когда в зону сварки поступает расплавленный присадочный материал, физический контакт между ним и свариваемыми кромками может осуществляться без приложения давления или при сравнительно небольшом давлении. Это относится к сварке нагретым газом и экструзионной сварке.
Установление физического контакта между свариваемыми поверхностями может предшествовать нагреву, осуществляться после нагрева соединяемых поверхностей до температур сварки или одновременно с нагревом. В любом случае на этой стадии происходит пластическое деформирование макр о- и микронеровностей, за счет чего происходит сближение контактирующих поверхностей. Работа деформации затрачивается также на удаление из контактной зоны инородных включений (газовых пузырей, масляных и жировых пятен и других загрязнений). Для мягких пластмасс и волокнистых материалов на этой стадии характерно уплотнение, проявляющееся в уменьшении толщины материала.
Активация свариваемых поверхностей включает в себя их нагрев для повышения энергии теплового движения макромолекул. Нагрев может осуществляться либо непосредственно за счет передачи тепла от нагретых инструмента, газа или присадочного материала к свариваемым деталям, либо за счет преобразования других видов энергии в тепловую. Это может быть механическая энергия ультразвуковых колебаний или трения, энергия высокочастотного электрического поля конденсатора, электромагнитная энергия, энергия инфракрасного излучения, лазера и кон-центрированного светового луча.
При сварке с использованием преобразования различных видов энергии в тепловую термической активации поверхностей будут предшествовать процессы, связанные со спецификой данного вида сварки: смещение диполей - при сварке токами высокой частоты; ввод и распространение ультразвуковых колебаний, а также концентрация и преобразование энергии механических колебаний в тепловую энергию - при ультразвуковой сварке; поглощение лучистой энергии - при сварке инфракрасным излучением.
Стадия термической активации может также сопровождаться развитием деформационных процессов, так как действие статической, а при ультразвуковой сварке и динамической нагрузок приводит к внедрению инструмента в поверхность соприкасающейся с ним детали, а также к вытеснению пластицированного или расплавленного материала из зоны сварки.
Объемное развитие взаимодействия сопровождается рядом сложных физико-химических процессов, среди которых наиболее существенными являются диффузия, течение и физико-химические превращения. Теория сварки, в которой главенствующая роль на этом этапе отводится диффузии, названа диффузионной. Теория, в которой считается, что ответственными за свариваемость являются процессы течения, названа реологической ~ по названию науки реологии, изучающей закономерности течения.
Согласно диффузионной теории, для получения соединения необходимо, чтобы при соприкосновении двух поверхностей вещества происходило достаточно полное их слияние (коалесценция).
Полная коалесценция двух слоев жидкости происходит при непосредственном их контакте и сопровождается исчезновением границы раздела между ними. В случае соединения полимеров одного контакта для коалесценции недостаточно, так как должно еще произойти структурообразование в зоне контакта, которое может быть достигнуто за счет диффузии макромолекул в целом или отдельных сегментов. Перемещению сегментов препятствуют их связи с остальной макромолекулой, поэтому диффузия сегментов вызывает некоторое изменение конфигурации цепной молекулы. В результате этого большое число последовательных перемещений сегментов будет приводить не только к изменению формы макромолекул, но и к смещению их центров тяжести. Перемещение сегментов и макромолекул в целом получило название микроброуновского и мак-роброуновского движения соответственно.
Перемещение макромолекул целиком особенно легко может происходить в том случае, если контакт слоев полимера осуществляется при температуре выше температуры течения. В этом случае в зоне контакта сравнительно легко возникает структура, характерная для полимера. Диффузия отдельных сегментов макромолекул может происходить и при температурах, отвечающих высокоэластическому состоянию полимера, при этом перемещение молекулы в целом затруднено. При таких температурах степень коалесценции меньше единицы (максимальная степень коалесценции равна единице и наблюдается только у жидкостей), ^го объясняется тем, что после перемещения сегментов на определенную глубину диффузия прекращается из-за напряжений, возникающих в молекулярных цепях.
Доказательством диффузионного характера процесса сварки может служить то обстоятельство, что все меры, способствующие тепловому движению (повышение давления и температуры, введение пластификаторов и т. д.), вызывают увеличение прочности сварного соединения и, наоборот, факторы, замедляющие диффузию, снижают прочность.
Сторонники реологической теории указывают, что если бы за образование соединения была ответственна только диффузия, то время сварки составляло бы десятки минут. Однако на практике это время значительно меньше. Кроме того, следует учитывать, что процессу диффузии неизбежно препятствуют воздушные прослойки и загрязнения поверхностных слоев свариваемых материалов, поэтому время проникновения еще более увеличивается. Наконец, следует иметь в виду, что коэффициент диффузии не остается постоянным, а непрерывно снижается, так как по мере проникновения участков макромолекул через границу раздела непрерывно возрастает их торможение.
Поэтому сторонники реологической теории предполагают, что проявлению сил межмолекулярного взаимодействия и диффузии в контактирующих объемах предшествует ряд явлений, связанных с течением и перемешиванием расплава (1-4, 16).
Считается, что при контакте расплавленных поверхностей напряжения, создаваемые усилием прижима (а при ультразвуковой сварке и динамические напряжения), вызывают сдвиг слоев расплава. При таком сдвиге происходит удаление из зоны соединения воздушной прослойки и других инородных включений, а расплав выдавливается из зоны сварки, что свидетельствует о получении качественного сварного соединения. Скорость сдвига на различных участках контактирующих поверхностей может различаться из-за неравномерности распределения температур и напряжений. Все это может привести к перемешиванию расплава в контактирующих объемах, что особенно вероятно в случаях сварки с использованием высокочастотных механических (ультразвуковая сварка) или электрических (сварка ТВЧ) колебаний.
Явление перемешивания вязкотекучего материала в зоне сварки подтверждено экспериментально при изучении процесса сварки пластмасс нагретым инструментом. По-видимому, для макро-объемов вязкотекучего материала при сварке характерен процесс перемешивания, а для микрообъемов - процесс диффузии.
Если сварка проводится в интервале температур высокоэластичности, преимущественным является диффузионный механизм. При этом необходим длительный контакт свариваемых поверхностей друг с другом, сварные швы сохраняют границу раздела, а материал в зоне соединения не отличается от исходного по надмолекулярной структуре. Такая сварка протекает при значительных давлениях, что обусловливает значительные остаточные напряжения в зоне шва после охлаждения соединения |7-10].
Если сварка проводится в интервале температур вязкотекучести (для аморфных полимеров) или в интервале температур плавления (для частично-кристаллических полимеров), процесс подобен сварке металлов. Под воздействием внешних сил происходит быстрая коалесценция расплава, сопровождающаяся перемещением и перемешиванием слоев. При этом слои расплава, содержащие газовые и оксидные включения, удаляются из зоны сварки, что облегчает дальнейшую взаимную диффузию участков молекулярных цепей и целых макромолекул в микрообъемах. В сварных швах таких соединений практически отсутствует граница раздела соединяемых поверхностей. Они не разрушаются по первоначальной плоскости контакта, а надмолекулярная структура может изменяться в зависимости от условий охлаждения расплава 19-11.
В связи с тем, что сварка плавлением на заключительном этапе связана с течением расплава, свариваемость пластмасс оценивают по таким характеристикам, как энергия активации вязкого течения, температурный интервал вязкотекучего состояния и вязкость расплава. В свете этих представлений становится очевидным, что чем меньше энергия активации вязкого течения и вязкость расплава и чем больше температурный интервал вяз-котекучести, тем более вероятно образование высококачественного сварного соединения. По реологическим свойствам пластмассы могут быть разделены на три группы (1, 4, 10, 16, 18, 19).
К первой группе можно отнести неориентированные термопласты, у которых энергия активации вязкого течения значительно меньше энергии химической связи и не превышает 150 кДж/моль; температурный интервал вязкотекучего состояния (Tт и Тр где Tт - температура текучести, а Тр- температура разложения) превышает 50 °С; вязкость расплава составляет 102-105 Па. с.
Такие термопласты при нагреве переходят в вязкотекучее состояние без термодеструкции и пребывают в вязкотекучем состоянии в достаточно широком интервале температур; при этом вязкость расплава такова, что при незначительных усилиях может быть обеспечена быстрая и полная его коалесценция. Эти термопласты хорошо свариваются плавлением различными методами сварки в широком интервале режимов. Наиболее типичные представители этой группы термопластов - полиолефины.
Ко второй группе можно отнести ориентированные термопласты с указанными выше реологическими свойствами; неориентированные и ориентированные термопласты с высокой энергией активации вязкого течения (близкой к энергии химической связи); термопласты с узким интервалом между температурой текучести и температурой разложения (менее 50 °С) и сравнительно высокой вязкостью расплавов.
Для термопластов с высокой энергией активации вязкого течения существует опасность деструкции при нагреве до вязкотекучего состояния. Термопласты с узким температурным интервалом между Tт и Тр могут разлагаться при незначительном перегреве. В ориентированных термопластах при нагреве до вязкотекучего состояния неизбежно нарушается ориентированная структура, обеспечивающая прочность материала. У термопластов с высокой вязкостью расплавов трудно обеспечить полную коалесценцию и перемешивание расплава.
Такие термопласты могут свариваться плавлением только при некоторых обязательных условиях. Для ориентированных материалов и материалов с узким интервалом между Tт и Тр сварка плавлением не должна вызывать разориентацию и деструкцию материала, что возможно только при условии быстрого и локального нагрева до температуры текучести свариваемых поверхностей без проплавления материала по всей толщине. Что касается термопластов с вязкостью расплавов выше 105 Па. с, то сварка их плавлением возможна только при условии снижения вязкости расплава в процессе сварки. Следовательно, для обеспечения возможности сварки плавлением термопластов, принадлежащих к этой группе, необходимо в каждом конкретном случае изыскивать оптимальные способы и технологические приемы сварки.
К этой группе относятся поливинилхлорид, поливинилиден-хлорид, пентапласт, полиэтилентерефталат, поликарбонат, плавкие фторопласты и другие термопласты.
К третьей группе относятся термопласты, энергия активации вязкого течения которых превышает энергию химической связи, а также термопласты с вязкостью расплава 1011 - 1012 Па. С. Эти термопласты не могут быть переведены в вязкотекучее состояние, т.е. не могут свариваться плавлением. К ним относятся, например, фторопласт-4, ацетат целлюлозы, поливинилацетат. Образование соединений таких термопластов возможно только по механизму диффузионной сварки с нагревом поверхностей до температур высокоэластического состояния, с длительной выдержкой под давлением, равным пределу вынужденной эластичности свариваемых материалов, при максимально возможной температуре.
Ускорение диффузионной сварки может быть достигнуто применением растворителей, в которых данный термопласт способен набухать и растворяться. Растворители увеличивают подвижность макромолекул, поэтому температура сварки может быть снижена.
СВАРКА ПРЯМЫМ НАГРЕВОМ ПРИ МОНТАЖЕ ТРУБОПРОВОДОВ
Сварка труб встык
П ластмассовые трубопроводы получили в последние годы широкое применение как у нас в стране, так и за рубежом. Такое широкое использование пластмассовых трубопроводов обусловлено тем, что они в-4-5 раз легче стальных, проявляют высокую стойкость к агрессивным средам и имеют меньшее гидравлическое сопротивление. Затраты труда на монтаж и эксплуатацию трубопроводов из пластмасс в среднем в 2 раза меньше, чем трубопроводов из углеродистых качественных сталей, и в 3-4 раза, - чем трубопроводов из нержавеющих сталей.
Наибольшее применение имеют трубы из полиэтилена низкой и высокой плотности, полипропилена и поливинилхлорида диаметром до 315 мм. В ближайшем будущем намечено применение труб из полиэтилена высокой плотности диаметром до 630 мм. Основной тип соединения таких труб при строительстве трубопроводов - сварка встык.
Таблица 4.1. Ориентировочные значения параметров режима сварки некоторых термопластов нагретым инструментом (прямым нагревом)
* Светостабилизирован техническим углеродом.
Высокое качество сварных соединений пластмассовых трубопроводов обеспечивается при проведении комплекса мероприятий по контролю на различных стадиях производства. Этот компле кс включает три этапа: предупредительный контроль (до начала сварки), активный (в процессе сварки) и приемочный (после завершения сварки) .
Предупредительный контроль включает в себя контроль качества свариваемых материалов, выбор сварочного оборудования с учетом показателей его эффективности, проверку квалификации сварщиков и контроль технологической подготовки производства.
При поступлении на склад необходимо сортировать трубы так, чтобы на сборку поступали трубы, близкие по геометрическим параметрам. На их поверхности и по торцам не должно быть трещин, пузырей, раковин и посторонних включений, видимых простым глазом, следов холодных спаев и разложения материала.
Условия хранения труб должны исключить попадание на них прямых солнечных лучей, так как при этом возможно не только снижение прочности материала труб, но и значительное ухудшение их свариваемости.
Перед сваркой трубы подвергаются механическим и термомеханическим испытаниям.
Гарантийный срок хранения труб - два года со дня изготовления. По истечении указанного срока трубы перед использованием должны подвергаться повторной проверке.
Большое значение имеет подготовка труб к сборке и сварке. Внутреннюю и наружную поверхности концов свариваемых труб на расстоянии не менее 30 мм от торца очищают от пыли, масла, технического углерода и других загрязнений, отрицательно влияющих на свариваемость и вызывающих растрескивание сварного шва в процессе эксплуатации. Соединяемые поверхности труб, зажатых в сварочной установке, после очистки подвергают торцовке. Стружку, образовавшуюся при торцовке, удаляют чистой тряпкой или другим способом, исключающим загрязнение торцов заготовок. В некоторых случаях применяется обезжиривание свариваемых концов растворителем (ацетоном, спиртом). Деформированные, порванные или имеющие забоины концы труб обрезаются. Режущий инструмент перед обработкой кромок должен быть обезжирен. Запрещается применять при этом охлаждающие эмульсии и смазки.
Следующими важными операциями являются сборка и центровка труб перед сваркой. Эти операции должны осуществляться на специальном устройстве или на установке, на которой будет вестись сварка. Концы стыкуемых труб должны крепиться в кольцевых зажимах (центраторах) сварочной установки таким образом, чтобы вылет труб составлял 60-70 мм. После сборки между обработанными торцами труб, приведенных в соприкосновение, не должно быть зазоров, превышающих 0,5 мм при диаметрах труб до 110 мм и 0,7 мм - при диаметрах более 110 мм. Смещение соединяемых концов труб, подготовленных к сварке, по наружному периметру не должно превышать 10% толщины стенки труб.
Контроль в процессе сварки проводится с целью строгого соблюдения основных параметров режима и цикла сварки. Ориентировочные значения основных параметров стыковой сварки труб прямым нагревом приведены в табл. 4.2 .
Основным параметром процесса является температура нагрева сварочного инструмента, которую необходимо поддерживать постоянной с точностью до ±10 К. Время нагрева - ©плавления торцов свариваемых труб сварочным инструментом - зависит от температуры окружающей среды, толщины стенки труб, подготовки торцов труб под сварку. Сокращение продолжительности нагрева при постоянной температуре инструмента приводит к недостаточному размягчению материала и, как следствие, к ухудшению качества сварного шва. Точное соблюдение времени нагрева не всегда гарантирует стабильную глубину прогрева, она может изменяться в зависимости от условий окружающей среды.
При нагреве сварочный инструмент должен касаться кромок труб по всему периметру. При правильном ведении процесса по всему периметру трубы должен образовываться равномерный грат расплавленного материала в виде валика высотой не более 2-3 мм.
После оплавления концов труб необходимо быстро удалить нагреватель и произвести осадку труб. Время между удалением нагревателя и осадкой труб не должно превышать 1-2 с, иначе происходит снижение прочности сварного шва в результате быстрого охлаждения свариваемых поверхностей. При увеличении давления происходит чрезмерное выдавливание оплавленного материала наружу и внутрь трубы, что ухудшает качество сварного соединения. Продолжительность охлаждения под давлением определяется с учетом толщины стенки свариваемых труб, температуры окружающего воздуха и типа пластмассы. Сваренный стык необходимо выдерживать под давлением до полного затвердевания материала, так как перемещение концов труб сразу же после сварки может привести к созданию в стыке дополнительных внутренних напряжений.
Таблица 42 . Ориентировочные значения параметров режима стыковой сварки труб нагретым инструментом
* НП и ПЭВП - полиэтилен низкой и высокой плотности соответственно; ПП - полипропилен; ПВХ - поливинилхлорид.
** при температуре окружающего воздуха 293 К.
Оставшийся после сварки на сварочном инструменте расплавленный материал необходимо удалить при помощи скребков, металлических щеток и ветоши.
Правильность соблюдения технологического процесса сварки может быть установлена по внешнему виду и форме сварного соединения. Наиболее высокое качество сварного соединения соответствует образованию двойного плавно скругленного валика грата равномерной по всему периметру шва толщины.
МС6-20 Технология сварки
Машины для сварки полиэтиленовых труб состоит из центратора, планшайбы, устанавливаемой на центраторе, торцевателя:
Центратор представляет из себя конструкцию из двух зажимных хомутов-неподвижная, закреплённая непосредственно на направляющих, и соустановленная с ней, подвижная. Подвижная каретка установлена с возможностью перемещения по двум направляющим с помощью двух гидроцилиндров приводимые в действие насосом. . Каретки выполнены в виде фиксированных нижних и верхних съёмных полухомутов, которые с помощью откидывающихся винтов имеют возможность зажимать свариваемые трубы. Для сварки труб различного диаметра машина снабжена сменными вкладышами, которые закрепляются винтами в полухомутах центратора.
Торцеватель состоит из двух соединённых между собой дисков, на которых закреплены по одному ножу. Посредством рукоятки с собачкой диски имеют возможность вращаться во втулках. Торцеватель снабжён двумя опорами, посредством которых торцеватель при работе устанавливается на направляющих центратора.
Планшайба предназначена для установки на ней фасонных изделий (втулок под фланец и переходов с D63 до 225мм), для крепления последних в планшайбе установлены прижимы. Они используются для центрирования и зажима переходов и втулок под фланец, при этом планшайба устанавливается и зажимается в подвижной каретке.
Работа машины заключается в центровке и фиксации свариваемых труб, подготовки торцев свариваемых труб к сварке, последующем нагревании торцев осадки стыка. В подготовку торцев труб входит очистка их от грязи, пыли и других веществ и последующее торцевание соединяемых поверхностей при помощи торцевателя. Торцы труб должны выступать от хомутов не более 55 -60 мм.
Подготовленные торцы труб нагреваются до температуры 220 С для ПНД и 200 С для ПВД. Нагрев производится нагревателем установленным между торцами свариваемых труб. Торцы труб в ручную подводятся к нагревателю (1 этап оплавления) с помощью гидропривода создаётся давление 0,49 Х 10... 0,78 X 10 Па (0,5...0,8 кгс/ см) обеспечивающее плотное прилегание торцев труб к плоскостям нагревателя (II этап оплавления). Необходимое давление контролируется установленными на насосе манометром.
По истечении заданного времени нагревания торцы труб отводят от нагревателя, убирают нагреватель и прижимают торцы труб друг другу с подъёмом давления до 2,00 Х 10 + 0,04 X 10 Па (2,0 + 0,04 кгс/ см) для труб ПНД и 0,98 Х 10 + 0,025 X 10 Па (1,0 + 0,025 кгс/ см) для труб ПВД.
Необходимое давление осадки выбирается по таблице 3. Справочному значению прибавляется усилие протяжки необходимое для сведения торцев плетей труб.
Затем идёт охлаждение сварного шва под давлением. Длительность этапов процесса сварки полиэтиленовых труб должна соответствовать таблице 3. Время оплавления 2-ого этапа оплавления при нагреве должно корректироваться в сторону увеличения зависимости от температуры окружающего воздуха (t окр.). Из расчёта 10 сек. на 1 градус при понижении температуры (нормальная температура эксплуатации 20° С).
Приварку производят при обратном ходе подвижной каретки (Разжим). Параметры сварки приведены в таблице
Состав
Принцип работы
ОСНОВНЫЕ ПОЛОЖЕНИЯ СТЫКОВОЙ СВАРКИ
С
вариваемые элементы должны быть совместимы в химическом и физическом отношении, указанная совместимость должна заверяться производителем труб и фитингов. Трубы должны иметь одинаковую толщину стенки и одинаковый диаметр.
Сварка осуществляется при соблюдении следующих условий:
В условиях низкой температуры, ветра, запыленности и загрязненности необходимо использовать палатку (при низких температурах - обогреваемую) для создания защищенной площадки для проведения сварочных работ. На сварных соединениях следует проводить тесты, позволяющие убедиться, достаточны ли принятые меры.
Концы труб должны оставаться чистыми до этапа сварки включительно.
Во время сварки концы труб должны нагреваться до одинаковой температуры (использовать защиту от солнечных лучей).
Во время сварки (и особенно на этапе остывания) исключить любое механическое воздействие.
Концы труб, не задействованные в сварочном процессе, должны быть закрыты заглушками во избежание охлаждения притоком воздуха.
Общие положения
Принцип сварки заключается в следующем: свариваемые поверхности прижимаются к термоэлементу (при определенном давлении, в течение определенного времени). Когда грат достиг определенной нормативами высоты, термоэлемент извлекается, и свариваемые детали соединяются (под давлением в течение некоторого времени).
Принцип и различные этапы сварки встык.
Выделяют 5 этапов цикла сварки:
- Этап оплавления (образования грата)
- Этап нагрева
- Этап выброса термоэлемента (зеркала)
- Этап сварки
- Этап охлаждения
Время и давление различны в зависимости от нормативов. Далее приводятся основные этапы сварочного цикла и их цели.
Этап оплавления:
На данном этапе происходит процесс образования грата. Он идет вслед за подготовкой свариваемых элементов (позиционированием, торцеванием, расчетом параметров, нагреванием до необходимой для сварки температуры) и позволяет удалить оставшиеся при обработке мелкие частицы.
Этап нагрева:
На данном этапе температура распространяется внутрь материала, происходит глубокое прогревание. В основном, давление при этом близко к нулю (оно должно лишь компенсировать силу сопротивления движению, чтобы свариваемые поверхности не отстояли от нагревательного элемента).
Этап выброса термоэлемента:
На данном этапе происходит выброс зеркала и соединение поверхностей сварки. Данный этап должен быть как можно короче, чтобы избежать потери температуры и снизить риск попадания посторонних частиц, которые могут повлиять на качество сварного соединения (пыль, песок...)
Этап сварки:
На этом этапе образуется окончательный грат и молекулярные связи, обеспечивающие однородность соединения.
Этап охлаждения:
По окончании сварки данный этап позволяет избежать напряжений или ударов, способных нарушить прочность соединения.
Различные нормы сварки встык.
Время и давление зависят от используемых нормативных документов. Далее приведены этапы сварочного цикла и значения времени и давление на каждом из них.
е - толщина стенки, Dn - номинальный диаметр, S - поверхность сварки, fct (: зависим. от)
Температура нагреват. элемента | P1 | t1 | P2 | t2 | t3 | P4 | t4 | P5 | t5 | |
DVS 2207 1995 e < 70mm | 200 C- 220 C | 0,15 Mpa | 0,5- 4 mm |
0 Mpa | 10e | Fct(e) | 0,15 Mpa | Fct(e) | ||
DVS 2207 1995 e <50mm | 195 C- 220 C | 0,15 Mpa | 0,5 - 3,5 mm |
0 Mpa | 190 -xxxs | Fct(e) | 0,15 Mpa | Fct(e) | ||
WRCWIS e>20mm | 230 C +-10 | 0,15 Mpa | Грат = 2 mm |
0 Mpa | 10e | 0,15 Mpa | 10 s | 0,15 Mpa | 50 e | |
DS/INF | 200 C- 220 C | 0,18 Mpa | Грат = 0,5 + 0,1e |
0,01 Mpa | 15e | 3+ 0,01 Dn | 0,18 Mpa | 3 + 0,03 Dn | 0,18 Mpa | 10s + 0,5e |
VEG 85 NEN 7200 | 210 C +-10 | 0,18 Mpa | Грат = 0,5 + 0,1e |
0 Mpa | 12e | 3+ 0,01 Dn | 0,18 Mpa | 3 + 0,03 Dn | 0,18 Mpa | 10s + 0,5e |
Electrabel Becetel I 110-250mm | 210 C +-10 | 0,05 Mpa | 10e | < 3s | 0,3 Mpa | Fct(S) | ||||
Electrabel Becetel I 250-315 | 210 C +-10 | 0,05 Mpa | 10e | < 3s | 0,24 Mpa | 10 s | 0,05 Mpa | Fct (S) | ||
GASTEC | 220 C +-15 | 0,18 Mpa | Грат = 0,5 + 0,1e |
0,01 Mpa | 12e | 4 + 0,01 e | 0,18 Mpa (4+0,03e) | 3+e min | 0,01 Mpa | 1,5e min |
GAZ Natural Si Dn=315 | 225 C +-15 | 0,18 Mpa | 1-2mm или 2-3 mm если DN 160 |
0,03 00,2 Mpa | Dn/2 + 30 +- 10 | Dn 4 < 200 5 >250 6 |
0,18 Mpa | >10min | 1,5e min c max 20 min |
НОРМЫ UNI:
e: Толщина трубы
Dn: Номинальный диаметр
b: высота грата = 0,5 + (0,1е) мм
t1: время обр.грата = fct (b) = 0,5 + (0,1е) мм
t2: время нагрева = 12е
t3: максимальное время выброса зеркала = 4 + (0,3е) сек
t4: максимальное время роста давления = 4 + (0,4е) сек
t5: время сварки = (3 + е) мин
t6: время охлаждения = (1,5е) мин
Для сварки труб и фитингов, у которых стенки больше или равны 20мм, добавляется фаза 6, в остальных случаях она включена в фазу 5.
S = Площадь сварки в мм2 = Pi(Dn2 - Di2)/4
Sc = Площадь цилиндра машины в мм2
e: Толщина трубы
Dn: Номинальный диаметр
Di: Внутренний диаметр (Dn-2e)
Sc: Площадь цилиндра машины в мм2 (4,32 см2, 5,88 см2, 8,46 см2)
b: высота шва = 0,5 + (0,1е) мм
T: Температура нагревательного элемента
P1: Давление образ.грата = 0,15 (S/Sc) х 10 (бар)
P2: Давление нагрева = 0,02 (S/Sc) х 10 (бар)
P5: Давление Сварки = 0,15 (S/Sc) х 10 (бар)
Р6: Давление охлаждения = если е 20 мм 0
если е 20 мм 0,05 (S/Sc) х 10 (бар)
t1: время образ.грата = fct (b) = 0,5 + (0,1е) мм
t2: время нагрева = (10t) + 60 сек
t3: максимальное время выброса зеркала = 10 сек
t4: 10 сек
t5: время сварки = если е 20 мм (3 + е) мин
если е 20 мм 10 сек
t6: время охлаждения = если е 20 мм= 0
если е 20 мм= (3 + е) мин
Для расчета принимаем значения:
S = Площадь сварки в мм2 = Pi(Dn2 - Di2)/4
Sc = Площадь цилиндра машины в мм2
e: Толщина трубы
Dn: Номинальный диаметр
Di: Внутренний диаметр (Dn-2e)
Sc: Площадь цилиндра машины в мм2 (4,32 см2, 5,88 см2, 8,46 см2)
b: высота грата= 0,5 + (0,1е) мм
T: Температура нагревательного элемента: Смотри таблицу
P1: Давление оплавления = 0,15 (S/Sc) х 10 (бар)
P2: Давление нагрева = 0,02 (S/Sc) х 10 (бар)
P5: Давление Сварка-Охлаждение = 0,15 (S/Sc) х 10 (бар)
t1: время оплавления = Смотри таблицу
t2: время нагрева = Смотри таблицу
t3: максимальное время выброса зеркала = Смотри таблицу
t4: максимальное время сдавливания = Смотри таблицу
t5: время сварки = Смотри таблицу
Муфтовая или раструбная сварка
1. НАЗНАЧЕНИЕ
Машина сварочная для сварки полиэтиленовых труб диаметром 50- 110 мм МС5-10 служит для сборки, фиксации и контактной сварки промышленных трубопроводов диаметром 50, 63, 75, 90, и 110 мм, а также для изготовления секционных отводов диаметром 50, 63, 75, 90 и 110 мм.
Машина изготавливается в климатическом исполнении " У1 " по ГОСТ 15150-69.
2. ТЕХНИЧЕСКИЕ ХАРАКТЕРИСТИКИ
Рабочий сваривает пнд трубу
Содержание статьи:
ПНД трубы с диаметром от 20 до 1200мм часто применяют благодаря легкости монтажа. Данные трубки могут быть как напорными так и безнапорными. Существуют разъемные способы соединения труб (соединение фланцами и фитингом), а также неразъемные такие как: стыковая сварка полиэтиленовых трубных изделий, в котором применяю аппарат для стыковой сварки, а также соединение полиэтиленовых труб муфтами. В зависимости от того в каких условиях будет проходить эксплуатация применяют определенный вид соединения трубопровода. Сварка пнд труб является наиболее надежным способом.
Сварка труб пнд: технология и применение.
В случае если система будет находиться по давлением обычно используют сварку пнд труб своими руками.
Применятся сварка полиэтиленовых труб различных видов:
- стыковая сварка;
- электромуфтовая сварка;
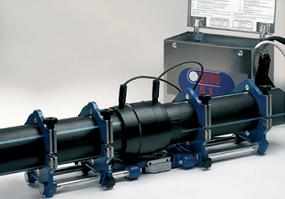
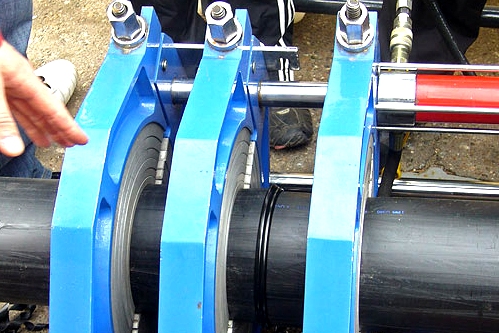
Перед тем как будет проведена сварка пнд труб своими руками , нужно все приготовить:
- Обработать механическим путем зоны будущого соединения сварки пнд встык;
- Проверяется оборудование для сварки труб пнд. Тут остановимся более детально;
- следует визуально проверить устройство на исправность;
- заправить топливом электрогенератор, провести его тестовый запуск;
- следует отчистить скребок, торцеватель и другие узлы от прилипшего полиэтилена;
- проверьте количество масла на гидросистеме.
Стыковая сварка пнд
Сварка пнд труб встык своими руками тяжелее производится, чем электромуфтовая. Беритесь за процесс если вы уверенны в своих силах и у вас есть квалификация сварщика, а также опыт. Отметим что сварка является экономически процессом потребляющим мало электроенергии.
Аппарат стыковой сварки пнд формирует монолитный шов, равный по качеству и свойствам основному материалу. Осуществляется таким образом соединение полиэтиленовых труб, фитингов и.т.д. Этот способ применим только для одинаковых марок и диаметра, с толщиной стенок не более 4.5 мм и диаметром более 50мм. Температура сварки пнд трубопровода также имеет значение, выполнять соединение следует в диапазоне температур от- 14С до +47С.
Температура сварки пнд труб в среднем составляет 130-140 градусов.
Способ предполагает наличие спец. оборудования.
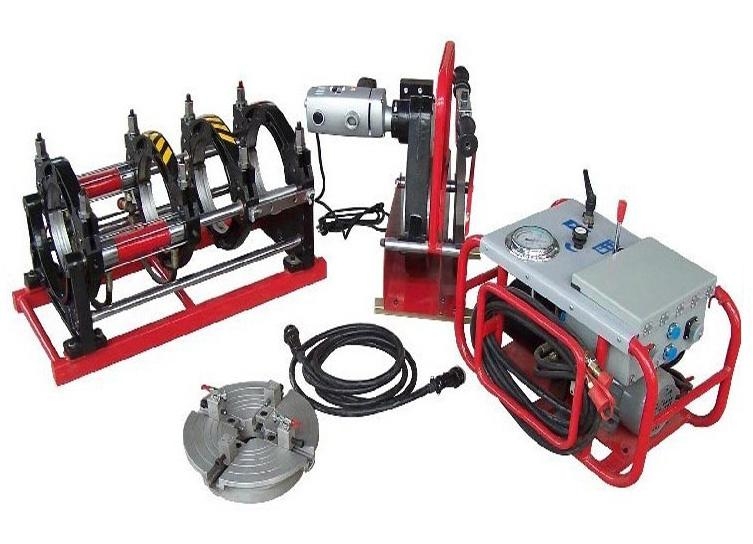
- Штангенциркуль- для измерения размеров материала;
- Центратор –для фиксациии сдавливания труб восевом направлении;\
- Торцеватель-для мех.. обработки;
- Гидравлический привод –для постоянного давления на трубы с точной регулировкой.
Стыковая сварка полиэтиленового провода: процедура и план действий
- проверяют овальность полиэтиленового изделия, соответствуют ли размеры, удаляют возможные неровности электроторцевателем;
- устанавливают трубы в центратор, соблюдая 4см растояния между торцами;
- далее следует расплавление торцов аппаратом для сварки, начинается процес плавления;
- Следует нагевать трубку в течении определенного времени, в соответствии, которое поможет выбрать таблица сварки пнд тркбопровода.
- Сразу после нагрева производиться соединение пнд встык нагретыми концами труб.
- далее аппарат стыковой сварки труб производт необходимое давление, после чего создается финальный грат.
После остывания полиэтилена создается бурт-герметичный шов. Следует не допускать сдигов стенки труб более чем на 9-10% от их толщины.
Таблицы сварки полиэтиленовых труб
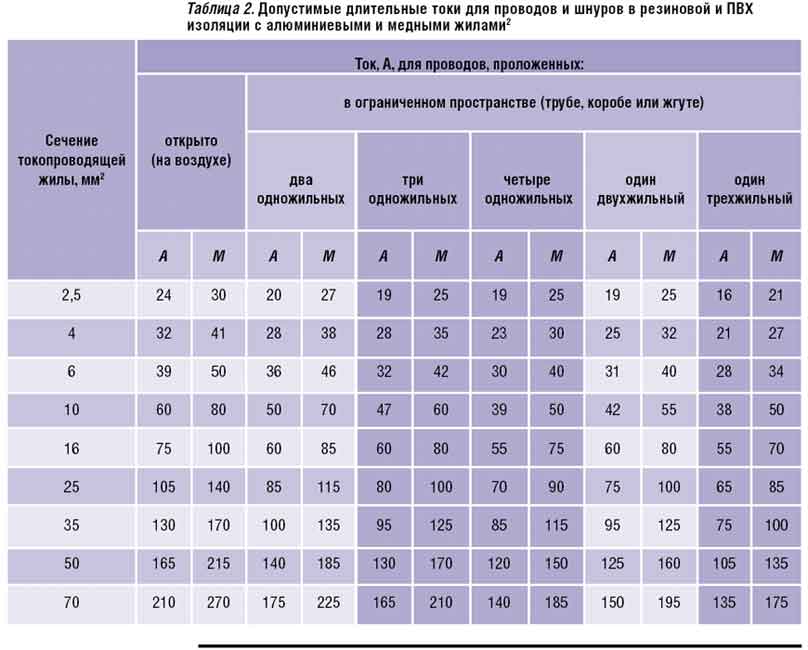
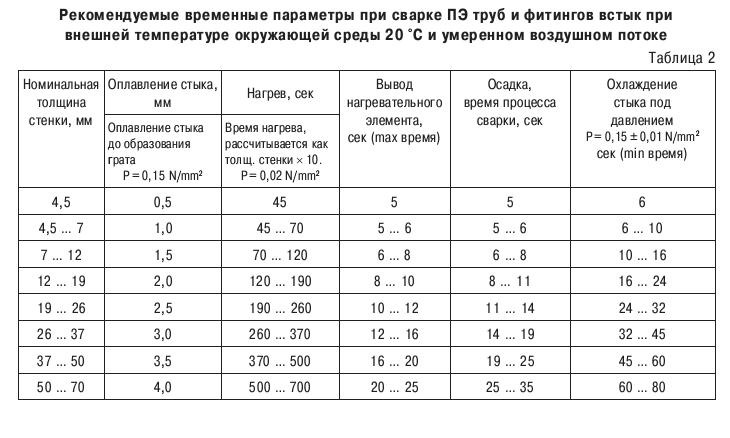
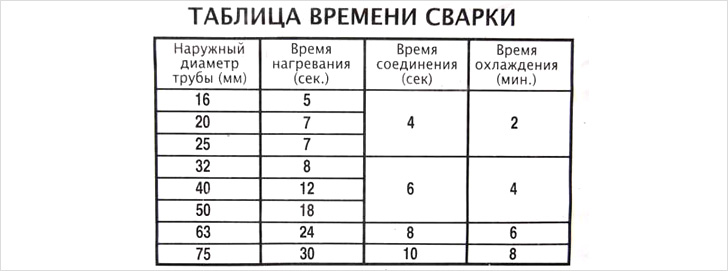
Видео-Сварка полиэтиленовых труб
Сварка полиэтиленовых труб муфтами
Этот способ менее выгоден с экономической точки зрения, но удобен в условиях малого пространства. Электромуфтовая сварка полиэтиленовых труб часто применяется во время ремонта, это первостепенно для провода до 150-160 мм в диаметре. Если следует создать дополнительный рукав тут этот метод также будет удобным. Грамотно созданное соединение выдержит 14-16 атмосфер давления.
Сварка муфт пнд
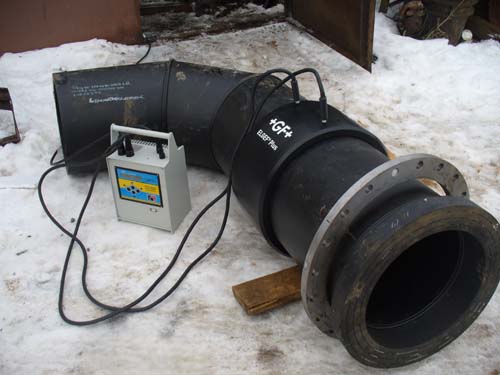
Электромуфта является фасонной деталью различных размеров из пнд материала внутри которой находятся электрические спирали. Существуют различные ее формы для различных видов соединения.
Создание сварочного шва:
- удаление загрязнения труб от жира и других нежелательных веществ;
- на сприраль муфты подается электрический ток что повышает температуру поэтилена и плавит его.
- далее нагреваються торцы под. муфтой
- трубопровод расширяется создавая тем самым необходимое для сварки давление.
- электричество отключается и свариваемая пнд труба остывает, тем самым образовывается надежное герметичное соединение. После остывания, ее извлекают и делают печать документа- протокол электросварки.
Видео-Электромуфтовая сварка труб пнд.
Видео-инструкция
Сварка пнд: цена, аренда
Многие фирмы в крупных городах предлагают услугу-аренду аппарата для сварки пнд труб. Пользователь избегает необходимости купить аппарат для сварки, и получить его во временное пользование, сэкономив средства.
Преимущества аренды аппарата для сварки.
- спец. оборудование довольно дорогое, аренда позволяет экономить;
- есть большой выбор техники в соответствии с вашими меняющимися запросами.
Стоимость аренды колеблется от 2 до 4 тысяч рублей в сутки.